Redesign of Cutler Hammer Crane Brakes Provides Major Saving
Author - Sam Megharaj Technical Services Engineer
CBC Bearings and Power Transmission as a specialist designer, supplier and installer of industrial brake systems offer the option to supply brakes from the worlds leading manufacturers to not only save costs but improve safety and power efficiency while conforming to the Australia crane code.
The following is an example of CBC’s redesign of an industrial braking system addressing a high cost critical issue for Hazelwood International Power in Victoria.
The braking system on the central hatchway hoist Thruster involved a Cutler Hammer electro magnet drum braking system including a Sonnerdale David Brown GR series gear coupling.
The arrangement needed extensive parts replacement which are not readily available and very expensive. The Sonnerdale David Brown GR series gear coupling had suffered server wear due to the difficulty of lubricating the coupling in the application with the correct grease volume and specification.
A summary of the procedure undertaken is as follows:
- Existing Brake unit: 203 mm Diameter Cutler Hammer electro magnet drum brake unit.
- Existing Coupling: 203 mm Diameter Sonnerdale David Brown GD series Gearflex brake drum coupling.
- Set Up: Main Hoist Drive brake unit.
- Brake Location: Between Motor and Gearbox (High speed Brake unit).
- Replacement Brake: CBC YW 200ED 30/05 Thruster brake unit on a 200 mm brake drum to current DIN 15435 standard.
- Replacement Drum coupling DIN 15430 standard 200 mm brake drum unit supplied with KTR brand coupling, SBN series modified adaptor brake drum.
Brake Commissioning and Set up Brake Drum Coupling:
- Existing brake drum surface coated with disintegrated grease, created issued with brake pad friction.
- Formed Gear tooth - disintegrated grease solidifying within the coupling outer sleeve resulting in gear failures.
- Due to Drum being located between 2 half gear coupling sleeves, the whole unit including the brake had to be dismantled to get accesses to inspect the teeth on the flex element.
Solution
Replaced Current set up with a KTR brand Flex spider brake drum coupling, with brake drum mounted in between coupling flange and the gearbox input hub half and spider located between intermediate half of the coupling and hub on the motor input shaft.
Advantages gained
- Maintenance free coupling, with easy removal of motor by just sliding the motor half with the hub connected to the shaft.
- In the event of power failure brake ON to the drum, as it is connected to the gearbox input shaft and no need of releasing the brake unit to access the coupling and loaded hook is still under the event of failsafe action.
Thruster Drum Brake unit - Existing Cutler Hammer brake, recent issues with parts and availability.
- Cutler Hammer brakes are made to Association of Iron and Steel Engineers (AISE) standards and Current Drum brake standards Australia follows is DIN standard. CBC designs related to crane brakes must meet the Australian crane code.
- Expensive Magnet coils and to refurbish coils with Full load test certificates also expensive.
Solution
CBC, have engineered adapter plates to conform to existing hole dimensions to suit Cutler Hammer base plate pattern and have adjusted centre heights and made up adapter plates to replace Cutler Hammer, Witton Kramer, Elevenja brakes and Sonnerdale David Brown brakes – JK series brakes, that are manufactured to AISE standards. The adaptor plate design has allowed CBC to adapt DIN standard replacement brakes such as Galvi, Bubenzer, SIBRE brakes on Cranes and other Material Handling and conveying applications.
CBC engineers have assisted in undertaking brake calculations based on the current Cuttler Hammer set up, Motor power, Speed, winch Drum specifications, crane capacity, Gearbox ratio and output speed, Max hook travel/speed and other crane parameters.
The CBC solution is a brake unit specified that meets the Australia Crane Code requirement for crane brakes.
CBC personnel working on the crane brake application setting up the DIN standard 200mm YW200 ED 30/05 thruster drum brake unit.
Existing Cutler Hammer brake being removed.
Adapter plates to suit the Cutler Hammer crane brakes base plate dimensions without changing structural conformity.
CBC YW 200 DIN thruster brake unit with auto wear compensator, manual hand release in the event of thruster failure, brake open close limit switch, pad wear indication switch.
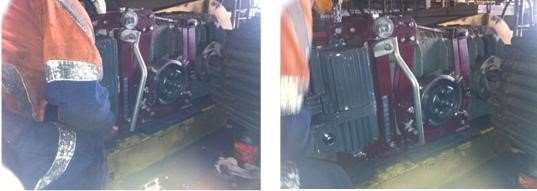
YW brake fitted and air gap adjusted between brake drum and brake shoes with help of manual hand release.
Cost Savings
To replace existing GD series Sonnerdale David Brown coupling with brake drum/drive: approx $3500 + GST including brake drum supplied with bore and key.
To perform an non destructive test (NDT) and report on the Cutler Hammer brakeunit, inspect, refurbish, reline brake shoes with new lining to suit industrial brake standards. Customer cost; approx $4500 + GST per brake per drive.
CBC are dealing with potential redesign of stage 2, stage 3 and stage 4 with similar set up and potential saving.
Total cost for qty 3 off drives (3 stages) $24,000 + GST
Solution from CBC
Brand new DIN 200mm brake unit, with KTR flex spider brake drum coupling, adaptor plates, onsite support (current project), CAD drawings, instruction and maintenance manual for both brake and coupling.
Price complete per drive for the above mentioned package $3750 + GST
Total cost for qty 3 off drives (3 stages) $11,250 + GST
Total cost saving on this crane brake project to date $4250 + GST per drive per hoist.
CBC supply technical support and service for a wide range of industrial braking systems including long travel brakes, box type brakes, hold brakes, tension brakes and emergency brakes.
This is backed with factory support from major brake manufacturers including Twiflex, Coremo and Transfluid.